Corrugated slitting blades are essential tools in the packaging and paper industry for cutting and slitting corrugated materials accurately and efficiently. Material selection for these blades is critical to ensuring optimal performance and longevity. Of the various materials available, it is generally accepted that the best material for corrugated slitting blades is tungsten carbide.
Corrugated slitting blades, also known as slitting knives, are designed to withstand the rigors of high-speed slitting and cutting processes. Tungsten carbide is a hard and dense material with several advantages that make it the first choice for making these blades.
So, what material is the best for Corrugated Slitting Blades?
Tungsten carbide has excellent wear resistance and is well suited to the demanding requirements of corrugated slitting operations. The abrasive characteristics of corrugated materials can quickly wear down traditional steel blades, resulting in frequent replacements and downtime. In contrast, corrugated slitting blades made from tungsten carbide can withstand extended use without significant wear, extending blade replacement intervals and increasing productivity.
Additionally, tungsten carbide’s inherent toughness provides excellent impact and impact resistance. This is especially important in high-speed slitting applications, where the blades are subjected to fast and powerful cutting actions. Tungsten carbide inserts are able to withstand such impacts without chipping or breaking, ensuring consistent and reliable performance, reducing the risk of production interruptions and maintenance costs.
In addition to durability, tungsten carbide blades help achieve a crisp, precise surface finish on corrugated materials. The sharp cutting edge and uniform wear resistance of these blades allow for clean, accurate slitting, resulting in a high-quality finished product. This is critical to meeting the stringent quality standards of the packaging and paper industry, where the appearance and integrity of the final product are critical.
The superior durability of tungsten carbide inserts results in extended service life, resulting in long-term cost savings and operational efficiencies. By reducing downtime for blade replacement and maintenance, manufacturers can optimize their production processes and minimize the total cost of ownership associated with slitting operations.
using tungsten carbide for corrugated slitting blades offers many advantages, including superior wear resistance, impact resistance, and service life. These qualities allow the blades to deliver a crisp finish and extend service life, ultimately helping to make corrugating operations more productive and cost-effective. Due to its outstanding performance and durability, tungsten carbide has become the material of choice for manufacturing corrugated slitting blades that meet the stringent requirements of the packaging and paper industry.
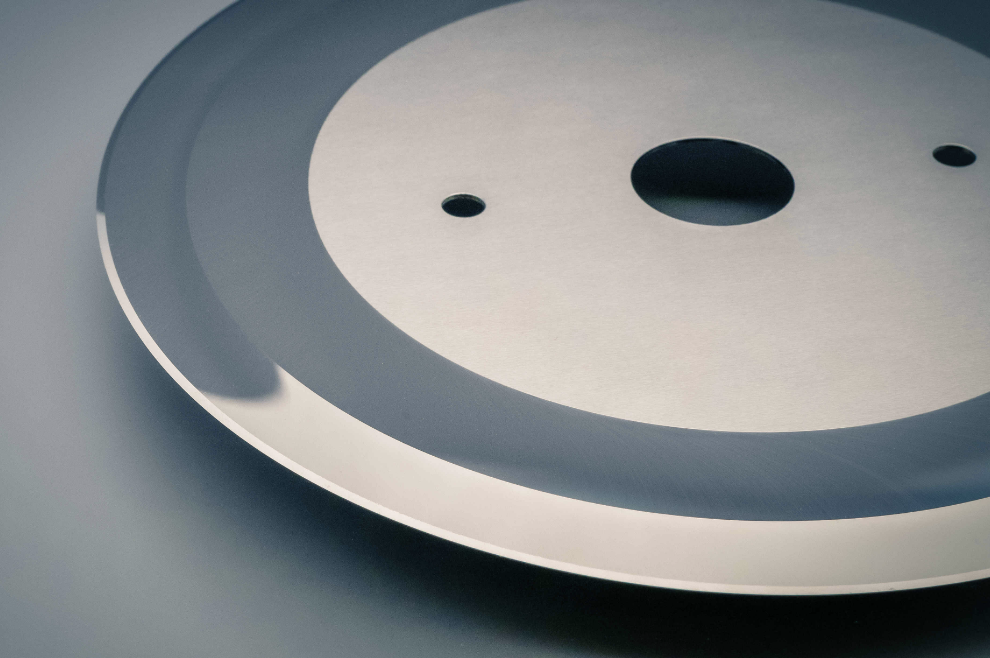
Post time: May-20-2024