Kedel Tools is a professional manufacturer of carbide products in China. With advanced equipment and a first-class technical production team, we produce and sell carbide products of various shapes, sizes, and brands, including CNC carbide inserts, turning inserts, milling inserts, threading inserts, grooving inserts, carbide end mills, carbide rotaryTungsten carbide rotary burrs are essential tools in various industries, providing precision and efficiency in shaping, deburring, and finishing tasks. Understanding their material composition and structure is crucial for appreciating their advantages over other alternatives.
Material Composition and Structure
Carbide rotary burrs are primarily composed of tungsten carbide (WC), a compound of tungsten and carbon renowned for its exceptional hardness and durability. This hardness is enhanced by the addition of cobalt (Co) as a binder, forming a cemented carbide structure. This combination ensures superior wear resistance and strength, making carbide rotary burrs ideal for demanding machining applications.
The structure of carbide rotary burrs typically consists of a solid carbide head attached to a shank. The head, available in various shapes such as cylindrical, ball, conical, and flame, is the working part of the burr. It is engineered with precision-cut flutes, spiral-shaped grooves that facilitate chip removal and prevent clogging during machining. The shank, usually made of steel or carbide, provides rigidity and support during operation. burrs, carbide plates, carbide rods, Carbide rings, carbide files, carbide end milling cutters and carbide milling cutters, and other non-standard carbide parts.
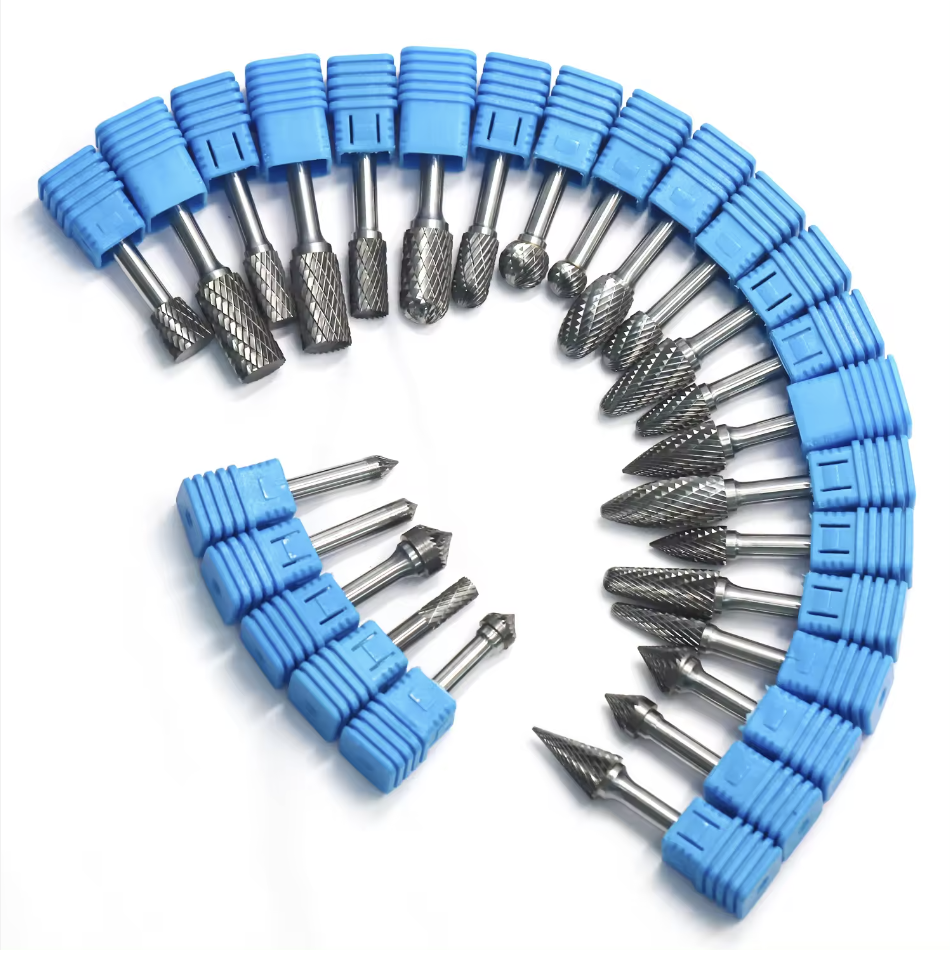
Advantages of Tungsten Carbide Rotary Burrs
Exceptional Hardness and Durability: Carbide rotary burrs are renowned for their exceptional hardness, ranking just below diamond on the Mohs scale. This hardness ensures prolonged tool life, even when cutting through tough materials like steel, stainless steel, cast iron, and non-ferrous metals. Their durability and resistance to wear make them indispensable in high-volume machining environments.
Versatility in Application: Carbide rotary burrs offer unmatched versatility, suitable for a wide range of applications across various industries. Whether shaping, deburring, grinding, or finishing, carbide rotary burrs excel in tasks on both flat and contoured surfaces. Their ability to work with different materials and geometries makes them essential tools in manufacturing and fabrication processes.
High Material Removal Rate: Carbide rotary burrs provide high material removal rates, making them highly efficient tools for machining operations. Their aggressive cutting action, combined with the precision of their design, allows for quick stock removal while maintaining dimensional accuracy and surface finish. This results in shorter machining times and increased productivity.
Heat and Wear Resistance: Carbide rotary burrs exhibit excellent heat and wear resistance, even under high speeds and temperatures. This resistance minimizes tool wear and ensures consistent performance throughout the machining process. Carbide rotary burrs can withstand the demanding conditions of prolonged use without sacrificing performance or quality.
Cost-Effectiveness: Despite their initial higher cost compared to some alternatives, carbide rotary burrs provide excellent long-term value. Their extended tool life and superior performance result in lower overall machining costs and increased efficiency in production processes. Investing in carbide rotary burrs translates into reduced downtime, increased productivity, and improved quality of finished products.
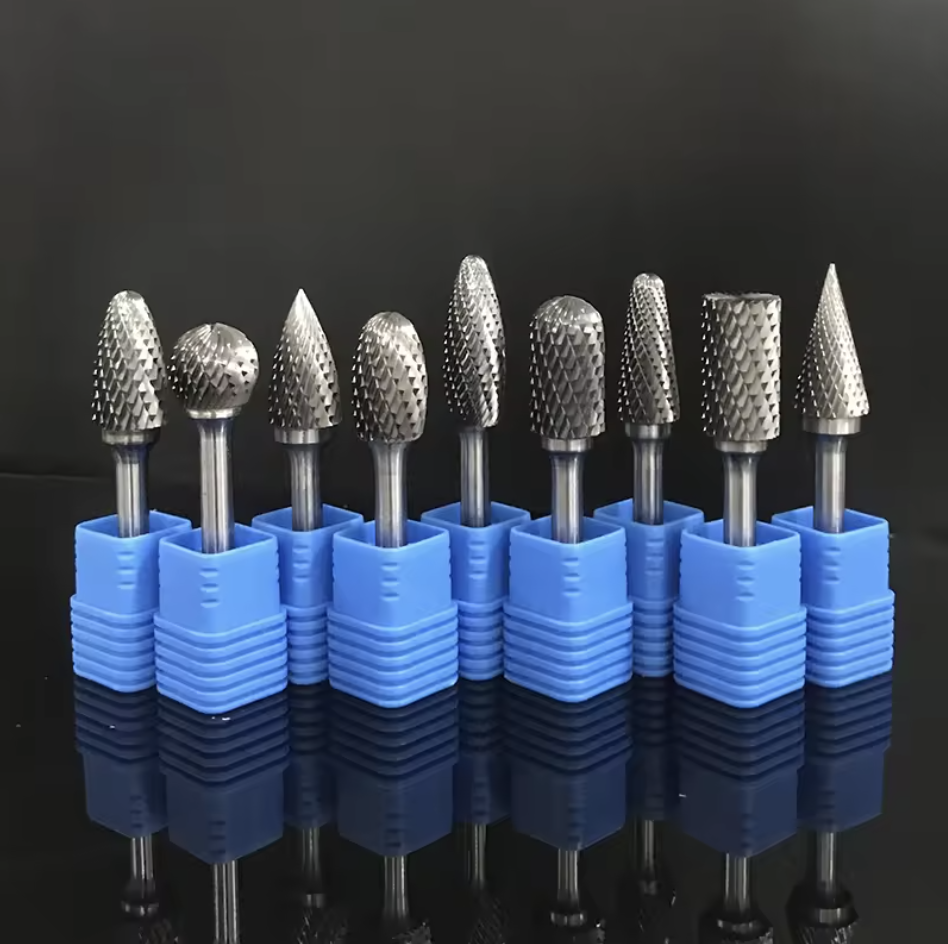
Post time: Apr-18-2024