When it comes to precision machining, the selection of the right carbide end mill plays a critical role in achieving optimal results. From function to characteristics, understanding the various aspects of carbide end mills is essential for choosing the right tool for the job.
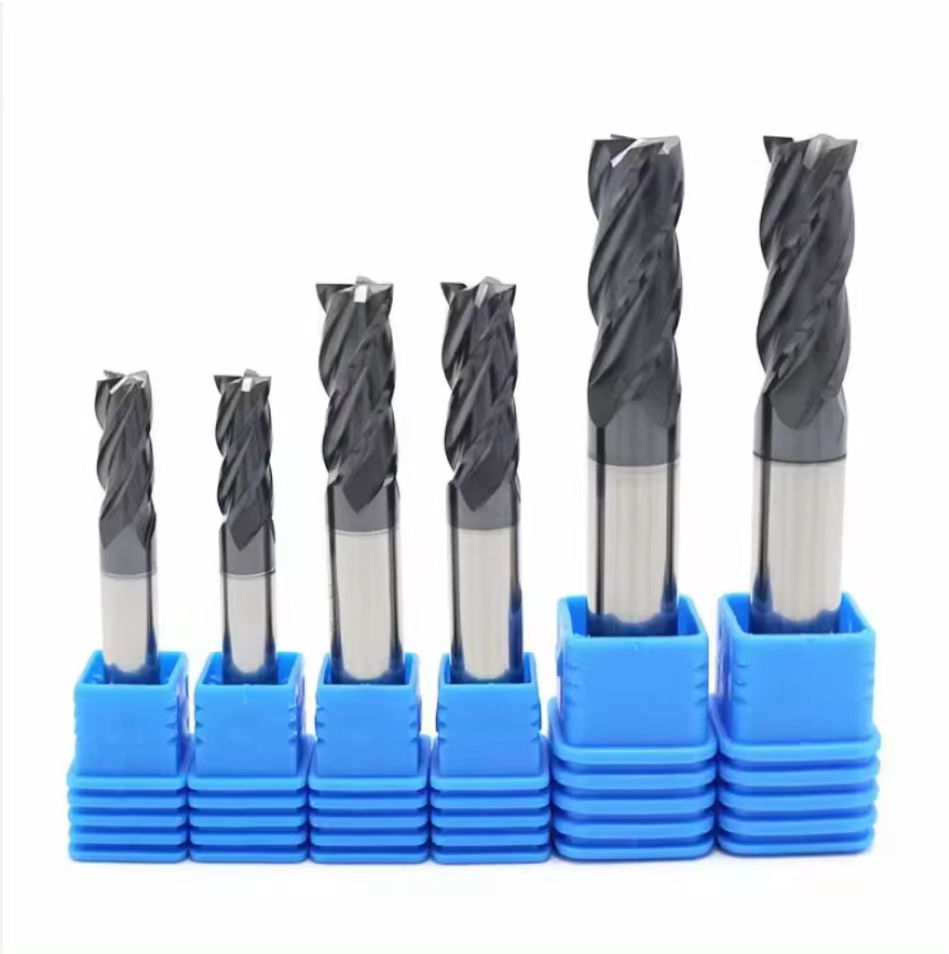
Carbide end mills are cutting tools used in milling applications to remove material from a workpiece. They feature sharp cutting edges made of tungsten carbide, which provide high hardness and wear resistance. The primary function of carbide end mills is to perform milling operations such as contouring, slotting, drilling, and profiling. With their ability to efficiently remove material from various workpiece materials, carbide end mills are indispensable in precision machining tasks.
Carbide end mills find applications across a wide range of industries, including aerospace, automotive, mold making, and general machining. They are suitable for machining materials such as aluminum, steel, stainless steel, titanium, and composite materials. Different types of carbide end mills are designed for specific applications. For instance, square end mills are ideal for general milling tasks, while ball nose end mills are suitable for contouring and 3D machining. Specialized end mills like roughing end mills and finishing end mills cater to specific machining requirements, offering versatility and efficiency.
Carbide end mills possess several key characteristics that make them superior tools for machining operations. First and foremost, their high hardness ensures prolonged tool life and consistent performance. The sharp cutting edges of carbide end mills deliver precise cuts and smooth finishes on workpieces. Additionally, carbide end mills offer excellent heat resistance, allowing for high-speed machining without compromising tool integrity. Their flute designs, such as helical and variable flute configurations, enable efficient chip evacuation and reduce cutting forces, resulting in improved surface quality and reduced machining time.
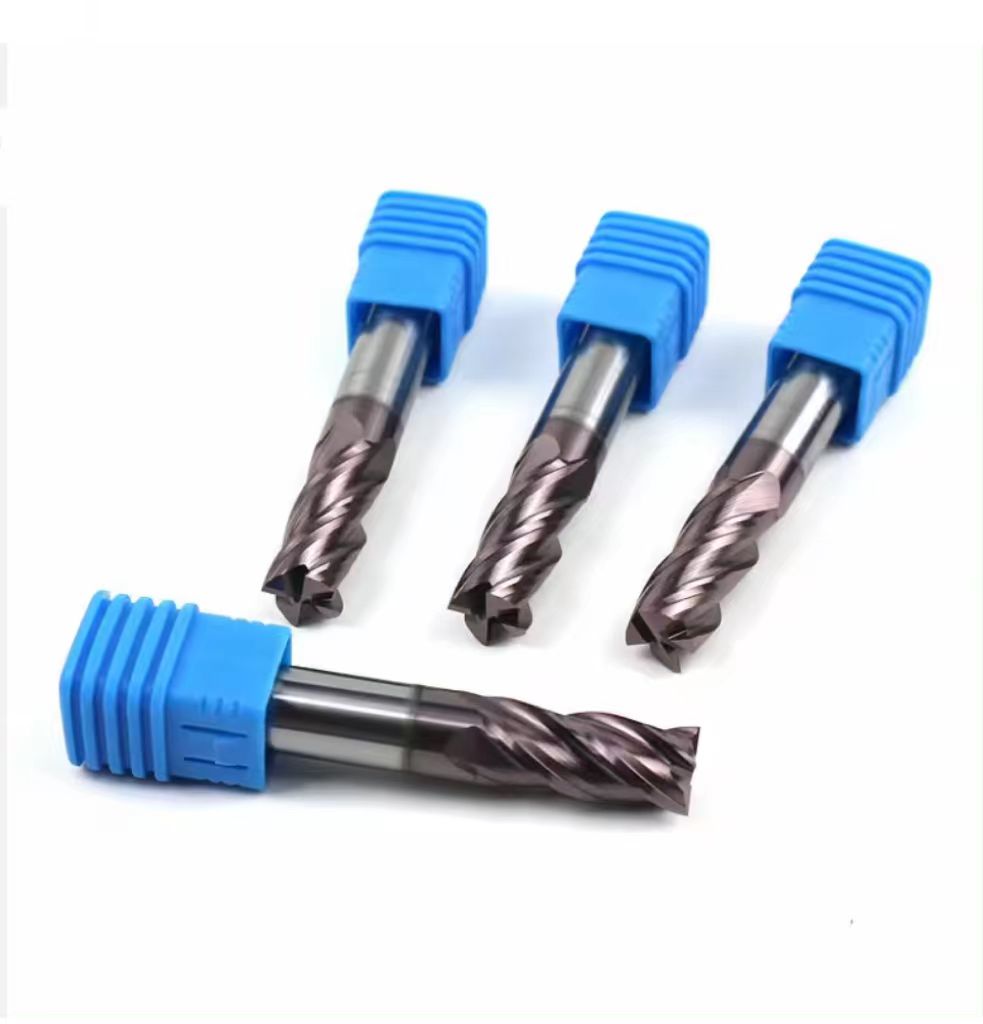
When selecting a carbide end mill, comprehensive considerations need to be made based on factors such as specific processing materials, processing technology, and processing accuracy. The first step is to select the tool material and tool type suitable for the material being processed to ensure that the tool can achieve the best cutting performance on the specific material. Secondly, we must consider the requirements of the processing technology and select the appropriate tool size, tool shape and number of tool teeth to ensure that the requirements for processing accuracy and surface finish can be met. Finally, the wear resistance and stability of the tool should be considered, and carbide end mills with longer service life and stable cutting performance should be selected to reduce production costs and improve processing efficiency.
Post time: Apr-24-2024